Hazardous chemicals and goods are part and parcel of thousands of workplaces across the globe. In fact, the Occupational Safety & Health Administration (OSHA), estimates there may be as many as 650,000 different hazardous chemical products at work in the United States. Every day, these products are put to use manufacturing goods, cleaning and disinfecting work surfaces, producing other chemicals, and performing a variety of other tasks.
Managing these hazardous materials in the workplace has always presented unique challenges and risks for employers and workers. According to OSHA, workers suffer more than 190,000 illnesses and 50,000 deaths annually due to chemical exposures. Violations relating to managing hazardous materials frequently draw multi-million dollar fines for organizations.
But due to a variety of new factors, these challenges are being further exacerbated and, unfortunately, OSHA records show there has been an increase in dangerous chemical incidents in recent years. In response to this worrying trend, OSHA has recently proposed major changes to regulations on how businesses must handle hazardous materials in the workplace.
It has never been more crucial for organizations to ensure that they are managing hazardous materials properly, to stay compliant, avoid fines, and most importantly, to protect their workforce.
A Change in Standards
OSHA’s most important standard surrounding chemical safety in the workplace is the Hazard Communication Standard (HCS), which is designed to ensure that information about chemical and toxic substance hazards and associated protective measures is disseminated to workers.
Organizations who have hazardous chemicals in their workplace need to maintain a written HazCom Plan, an up-to-date chemical inventory list, a library of SDSs for all hazardous chemicals that employees have access to without barriers, a system for managing shipped container labels, and workplace container labels and provide HazCom training to all employees who work with hazardous chemicals.
Due to the many risks and dangers that come with hazardous chemicals, however, chemical safety regulations are never static.
10 years ago in 2012, OSHA adopted elements of the United Nations' Globally Harmonized System of Classification and Labeling of Chemicals (GHS) into its Hazard Communication Standard. While U.S. workplaces adjusted to the new system — including new hazard labels, a new 16-section Safety Data Sheet format, and new hazard classifications — the GHS continued to evolve at the UN.
In February 2021, OSHA proposed new updates to the HCS to align it with the 7th edition of the GHS. While these most recent changes may not be as wide-ranging as the initial shift to the GHS system, there are still significant adjustments that companies should be preparing for.
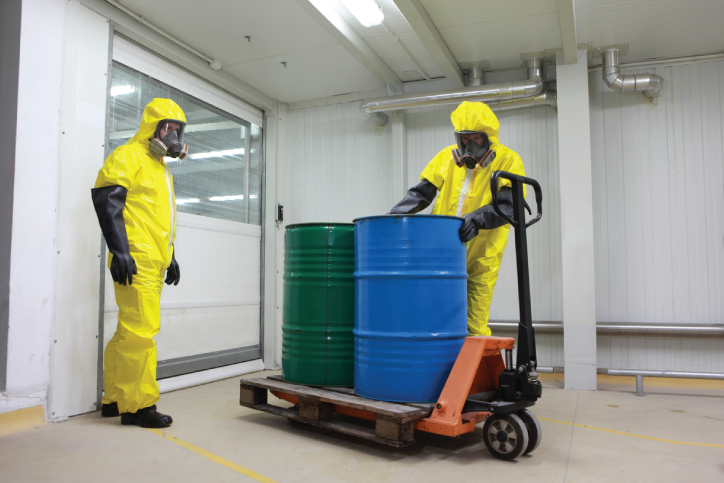
The Costs of Non-Compliance
Despite the potential severity of any fallout from a chemical-related incident, the Hazard Communication Standard is the second most frequently cited federal workplace safety and health standard, surpassed only by the construction industry’s fall protection standard. And fines and penalties for violations of the HCS can be particularly significant.
Just last year in 2021, there was a total of over $250 million dollars worth of fines, handed out for chemical-related incidents alone – evidence that regulators do not shy away from making examples out of the companies that fail in their duties to protect employees and the environment from hazardous chemicals.
Some of the biggest fines ever recorded in history are in relation to hazardous material impact on our global environment — The Deepwater Horizon Disaster in 2010, earned BP a fine of $13.8 billion dollars. But it is not just large enterprise companies that regulators look at. In 2021, a sub-3,000 employee company was fined $1.5 million dollars for chemical safety-related violations.
As inflation continues to rise, fines for chemical safety violations will continue to keep pace. Just in January of this year, we saw OSHA increase the maximum civil penalty for willful and repeat violations to $145,027. And climate change is only exacerbating these increasing fines, as the pressure to limit our environmental impact grows, regulators are cracking down on companies that are not falling in line.
But it is not only regulators' large monetary fines that companies should consider. The indirect costs of violating hazardous chemical regulations can also be severely detrimental. These include:
- Workers’ compensation claims from workers injured by chemical exposure
- Lost productivity during and after an incident
- Lowered workforce morale due to fear and uncertainty around chemical exposure
- Labor hours spent tracking down and applying labels
- Expenses of cleaning and replacing any damaged equipment after an accident due to hazard miscommunication
- Legal and compliance fees
- Negative publicity and reputational damage
-
Complex Challenges
Rules and regulations surrounding managing hazardous materials in the workplace are in place for very valid reasons; most crucially, to protect workers from injuries and death.
However, as we have just discussed, HazComm violations are still a very frequent occurrence — and when you take a closer look at the many complex challenges that come with trying to practice safe chemical management, it’s no surprise that many organizations, large and small, struggle to stay compliant and effectively protect their workers.
Vast Information
The importance of correct and consistent chemical labeling can not be overstated. But in complex working environments, such as laboratories, agriculture, or industrial production — where several chemicals are being used at once and in a fast-paced environment — chemical containers can sometimes be left open and unlabelled for periods of time.
When a worksite has multiple visitors, contractors, and new staff members coming and going, it can never be assumed that everyone has knowledge of what chemicals are stored where — which is why properly following the labeling requirements is paramount to creating a safe workplace.
Maintaining Correct Labeling
According to a study carried out by Ipsos Global Advisor, 71% of senior executive travelers reported they had experienced medical concerns abroad. Many countries don’t have the level of sanitation regulation we enjoy in the United States. Drinking the local water can cause illnesses. Other concerns include the level of protection from COVID-19, local epidemics, and the quality of local healthcare services.
Employee Desensitization
Thankfully, large-scale chemical incidents such as massive explosions or devastating leaks, do not happen very regularly. However, when employees are dealing with hazardous chemicals every day and are not often seeing the potentially damaging consequences of their dangers, they can become complacent and desensitized to the risks. And when complacency sets in, the importance of constant preventive and proactive measures can be lost or forgotten.
Staff Turnover
Another consistent challenge that employers have to contend with is the turnover of staff when trying to ensure that all employees are adequately trained.
Unfortunately, this strain on organizations is only being further exacerbated by the recent impacts of the so-called “Great Resignation.” According to the Society for Human Resource Management, “last year, 47.8 million workers quit their jobs, an average of nearly 4 million each month, meaning 2021 holds the highest average on record.” These unprecedented rates of staff movement mean that there is a vastly higher number of inexperienced employees in the workplace, and only organizations with the most effective and efficient training programs can manage these levels of turnover.
To add to these concerns, an aging workforce, with many pivotal team members approaching retirement or leaving for more senior roles, can create additional knowledge gaps across businesses. As the most trained and experienced staff leave, ensuring all new employees are brought up to speed quickly, and efficiently, is vital.
5 Steps to a Safer Workplace
Despite these challenges, there are steps that employers can take to ensure compliance, and most importantly, ensure the safety of their employees that are exposed to hazardous materials in the workplace.
When it comes to staying compliant with the Hazard Communication Standard, the best resource is the source itself: OSHA. And as this standard was specifically designed to protect workers, if you have prepared a comprehensive plan that aligns with the HCS, you should succeed in keeping your workforce safe. So let’s take a closer look at key elements within the HCS, and break them down into 5 simple, actionable steps:
Step 1: Prepare and implement a written Hazard Communication plan.
An employer must create a written hazard communication program that outlines the manner in which the employer will adhere to the labeling, SDS, and training and information requirements of the HCS. The program must also describe what risks employees face due to hazardous chemicals and how it will share information with employees about those risks and any potential health issues that could result.
Due to the significant level of detail required in a HazComm plan, a good place for a smaller organization to start would be with a generic plan created by an experienced third party, that can then be modified as needed to reflect the organization’s unique characteristics. By taking this approach, an organization can be sure to include all the required elements.
Step 2: Inventory all hazardous chemicals.
To comply with OSHA’s Hazard Communication Standard, you need to first understand the range of chemicals that you have on-site at your organization and so, an inventory should be taken of all the hazardous chemicals being used throughout your facility. All of the hazardous chemicals in your facility will need to be matched with complete, properly formatted SDSs.
Your chemical inventory management system should also include the following details:
- Location tracking
- Container tracking and reconciliation reporting
- Unit of measure conversions and calculations
- Material approval routings
- Key coManaging restricted and banned chemicals
- Notifications of exceeded thresholds
Step 3: Ensure that ALL chemical containers are always correctly labeled.
Employers must ensure that all hazardous material containers (including pipes, tanks, and secondary containers) are properly labeled, tagged, or marked with either the appropriate shipping labels or information regarding the chemical’s hazards. It is not required, but it is advisable to also label non-hazardous materials in order to avoid any confusion or uncertainty in an emergency situation.
Labels or other warnings must be legible in English and prominently displayed on the container or readily available in the work area. Employers may also add the information in other languages for workers who speak other languages, provided that the information is always presented in English as well.
A primary end goal of labeling chemicals should be that all employees, shipping personnel, and others who may come in contact with the chemicals can easily recognize what chemicals they are handling and quickly understand the hazardous risks involved.
Step 4: Establish and maintain a complete library of Safety Data Sheets (SDS).
Safety Data Sheets (SDS) communicate essential information about hazardous chemicals, including their properties and risks, correct handling and storage practices, and what protective measures employees should use to remain safe when handling or interacting with chemicals.
Employers must keep an SDS for all hazardous chemicals used in the workplace and ensure the information is readily accessible in the work area for staff who could encounter the chemical. Traditionally, this has been accomplished by managing physical copies of SDSs in three-ring binders. However, a more modern and cost-efficient method is to use an online software system that electronically manages these documents. A good chemical management software solution stores SDSs in a secure, cloud-based library and are mobile-enabled so employees can access them no matter where they are — even from remote, offline locations.
Step 5: Inform and train your workforce.
Regular and effective employee training is essential to the success of your Hazard Communication program. Workers must receive training in accessing and using the information on labels and SDSs. They must also be aware of the protective measures available in the workplace, how to use or implement these measures, who to contact if issues arise, and all other aspects of your HCS program.
OSHA requires organizations to provide hazard communication training at two different times. First, workers should receive training when they are initially assigned to a position where there is a potential for hazardous chemical exposure. Second, training should be required whenever there is a new hazardous chemical introduced in their work environment for which they have not been previously trained. However, more frequent ‘mini’ learning sessions and resources that are available to refer back to at any time, can make a huge difference to help workers retain information and create a more engaged safety culture.
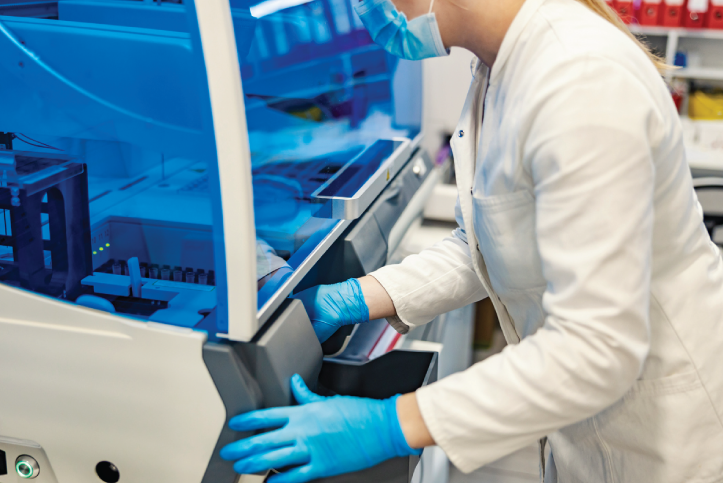
Hazardous Material Handling in the Digital Age
You have meticulously followed OSHA’s Hazard Communication Standard to a T, and you have carefully crafted, comprehensive safety plans, ready to protect your employees. But implementing, maintaining, and communicating these plans to the workforce can still seem like an overwhelming challenge.
How can organizations have peace of mind that their workforce has access to safety information, at any time? And that the information is always accurate and up to date? This is where mobile software can support and enhance your plans. In a crisis, a mobile phone is often the first and only thing a person will reach for. For this reason, it’s understandable why businesses are looking to mobile technology to put life-saving tools and information in their workforce's pockets.
Information Sharing
Mobile can break down huge amounts of information and segment it. The time spent searching through binders full of paper-based information such as SDSs, HazComm plans and emergency action plans can be reduced to seconds with mobile. Not only can this time saved improve efficiency and productivity in the workplace, but a fast reaction can significantly reduce the impacts of a hazardous material emergency. And with tools like QR code scanning and search functionality, end-users can access the information they need immediately, without having to wade through fluff or irrelevant information.
Accuracy
Mobile can also help to make sure the information you provide to employees is the most accurate version. By integrating with existing systems, you can manage updates in one place — creating a single source of truth. A good mobile app should automatically update to reflect those changes, without any manual input. Knowing that the information in employees' pockets is always up to date, gives peace of mind for leaders, and saves the time and money spent updating information manually.
Multiple Language Support
OSHA’s Training Standards Policy states that “an employer must instruct its employees using both a language and vocabulary that the employees can understand. For example, if an employee does not speak or comprehend English, instruction must be provided in a language the employee can understand.” An app that can easily contain content in multiple languages helps companies stay compliant and ensure inclusivity across the workforce.
Offline Accessibility
Industries such as construction, oil & gas, or agriculture, where employees typically work in more remote environments, don’t have to rely on a stable internet connection to be able to access critical information. Robust mobile technology can support native content that is available offline anytime, anywhere — which is paramount to further increase accessibility and stay compliant.
Interactive Training
Training doesn’t have to be a chore for employees. Forward-thinking companies are increasingly utilizing the multimedia power of mobile to enhance learning. Mobile can support high-quality and interactive training with features such as live polls, how-to-videos, flash quizzes, and more. This type of engaging training is proven to be better retained by employees, especially when it’s delivered on a tool that the modern worker is extremely familiar with.
With mobile, employees can also refer back to course material at any time which provides them with the flexibility to learn at their own pace and schedules — helping to minimize the impact of training on operations compared to live classroom training.