Recent headlines have been rife with reports of train derailments, hazardous material releases, and follow-up investigations by the National Transportation Safety Board (NTSB). These incidents remind us of the hazards and risks posed by the numerous chemicals and other hazardous materials transported daily across our nation’s rail system.
While perhaps less well known than the NTSB, the US Chemical Safety and Hazard Investigation Board – or CSB for short – has been operating since 1998. Since then CSB has been investigating industrial facility accidents and releases to determine and understand the underlying causes, and to make risk reduction recommendations to prevent future occurrences.
The CSB’s work focuses largely on Process Safety and, indeed, the focus is well warranted. Recently released CSB data sheds light on significant hazardous chemical releases – those that result in; one or more fatalities or hospitalizations, or $1M or more in related property damage. This data shows that 184 significant releases between January 2021 through December 2022 resulted in:
- 104 hospitalizations
- 84 property losses of $1M or more (each)
- 24 fatalities
Acronyms to keep in mind
The CSB investigates and issues process safety recommendations independent of the Occupational Safety and Health Administration (OSHA) and Environmental Protection Agency (EPA). OSHA’s Process Safety Management (PSM) and EPA’s analogous Risk Management Program (RMP) standards lay out the regulatory framework and management system approach that industrial facilities must follow. When implemented with rigor, these standards and frameworks enable organizations to reduce and control process safety-related risks, and ensure safe workplaces and surrounding communities.
This multi-part blog series focuses broadly on OSHA’s PSM standards and regulations. In the first installment we’ll discuss the background of the PSM standard, its applicability across various industries, PSM’s key elements, and suggested steps you can take to determine whether your facility may be covered by PSM. In the full series – An Introduction to OSHA’s Process Safety Management Standard – Paul Ahnberg shares his expertise from 32 years of EHS experience working across multiple PSM industries and manufacturing facilities.
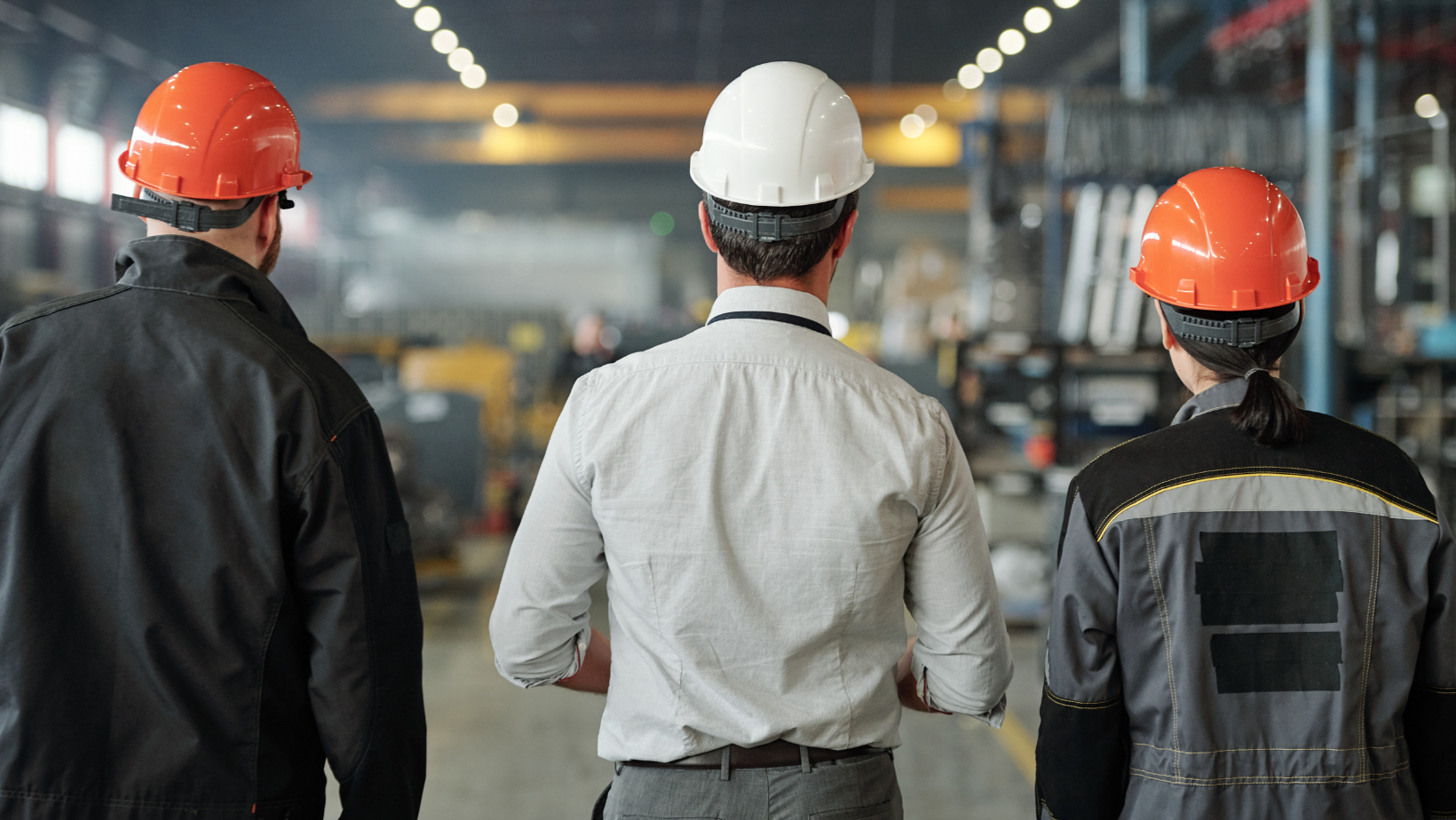
Background of OSHA PSM
In 1992, following a Congressional mandate via the 1990 Clean Air Act Amendments, OSHA’s PSM standard was promulgated and introduced the initial set of regulations and guidelines. The complete set of PSM regulations can be found at 29 CFR 1910.119 – Process Safety Management of Highly Hazardous Chemicals..
The primary goal of the PSM standard is to prevent or mitigate the hazards stemming from the catastrophic release of “highly hazardous chemicals from industrial processes – meaning chemicals that are flammable, explosive, reactive, and/or toxic. PSM applies to any facility with industrial processes that store, use, handle, manufacture, and/or move such chemicals in quantities exceeding specified threshold quantities. Examples of these chemicals include but are not limited to ammonia, chlorine, formaldehyde, and hydrogen sulfide. For the complete list of the 137 highly hazardous chemicals and their associated threshold quantities see 29 CFR 1910.119 Appendix A.
The PSM standard requires affected facilities to develop and implement a comprehensive management system to identify, evaluate, and control the hazards associated with their chemical processes. While the management system must address 14 specific elements, OSHA intended the PSM standard to be performance-based. This means facilities are allowed flexibility in how they tailor their specific PSM elements and safety programs to best address the hazards posed by their unique industrial processes.
Overall, PSM plays a crucial role in ensuring the safety and well-being of workers and communities near hazardous industrial processes. Properly implemented, PSM protects workers from incidents that can cause serious injuries, fatalities, and long-term health effects, and can help prevent environmental damage resulting from hazardous chemical releases that contaminate soil, water, and air, and have long-term effects on the environment.
In addition, by preventing incidents from occurring in the first place, PSM can help prevent or reduce facility costs related to hazardous chemical releases. For example - cleanup costs, legal fees, and lost productivity.
What Types of Facilities Need to Comply with PSM?
Compliance with OSHA’s PSM standard is mandatory for facilities with industrial processes that involve the storage, use, handling, manufacture, and/or onsite movement of highly hazardous chemicals at or above specified threshold quantities. For specific applicability requirements and definition of terms see 29 CFR 1910.119(a) and (b).
Covered facilities are considered high-risk because of their potential to cause catastrophic accidents. In practice, this means that a wide range of facilities and industries are required to comply. Following are specific examples:
- Chemical manufacturing and processing, including the production of a wide range of chemicals (acids, solvents, polymers, etc.);
- Petroleum refining and processing, including the refining of crude oil into various products (gasoline, diesel fuel, lubricants, etc.);
- Pesticides and agricultural chemicals manufacturing, including the production of pesticides, herbicides, and other agricultural chemicals;
- Paints, coatings, and adhesives manufacturing for various industries;
- Plastics and rubber products manufacturing, including the production of a wide range of plastic and rubber products (PVC pipes, automotive parts, medical devices, etc.);
- Explosives manufacturing, including production for mining, demolition, and military applications;
- Ammonia refrigeration systems, including the use of ammonia as a refrigerant in industrial refrigeration systems;
- Energy production, including electricity generation and natural gas processing for the production of electricity, natural gas, and other energy products;
- Pulp and paper manufacturing, including paper products (newspapers, cardboard, etc.);
- Water and wastewater treatment facilities, including the treatment of water and wastewater using chemicals and other hazardous materials;
- Metal production and processing, including aluminum, steel and various metals and metal products; and
- Semiconductor manufacturing, including the production of semiconductors and other electronic components.
It is important to note that the PSM standard applies to any facility, regardless of industry, that uses highly hazardous chemicals in their processes and meets the quantity thresholds specified in the standard.
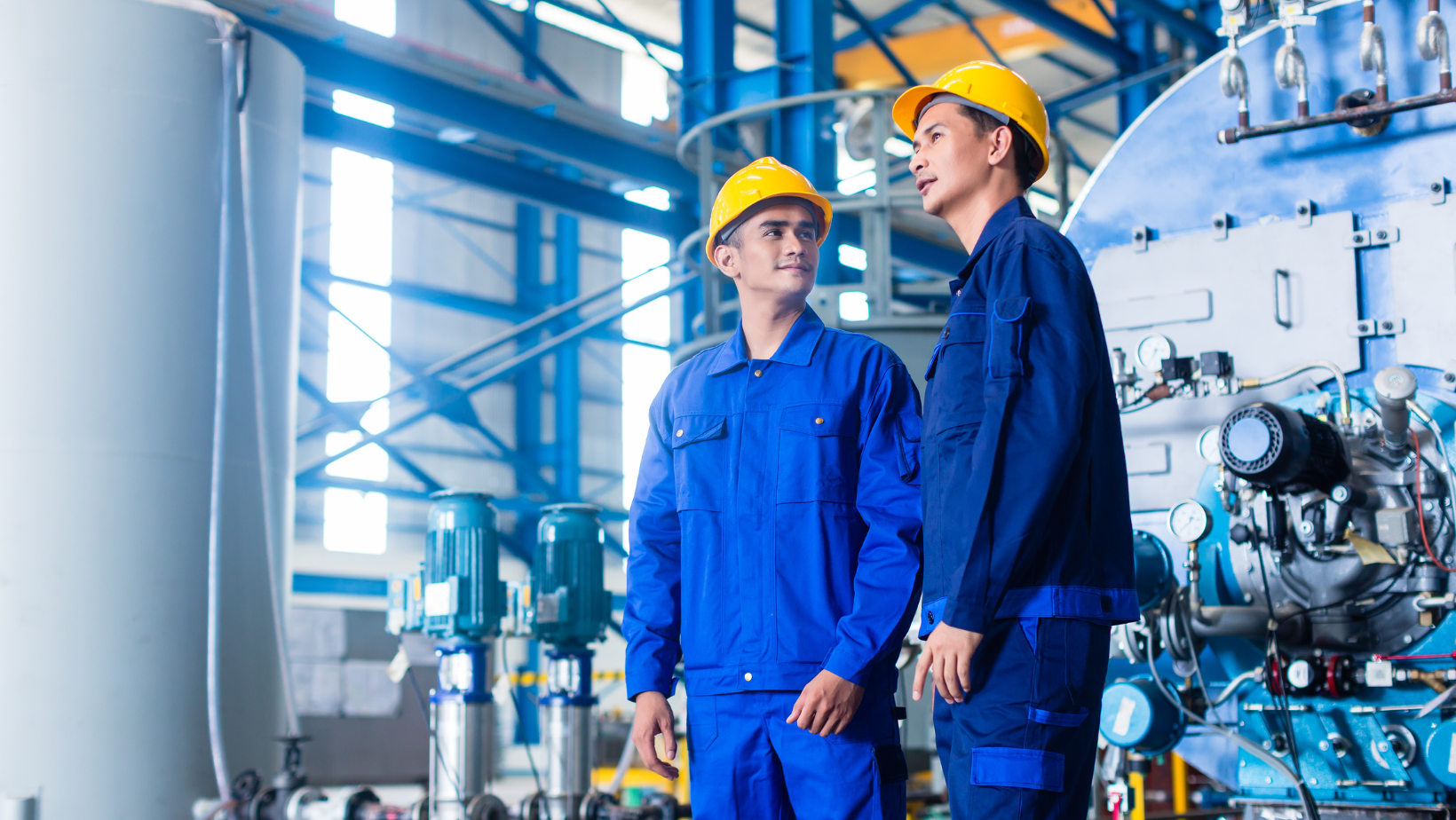
What are the 14 PSM management system elements?
OSHA’s PSM management system standard includes 14 mandatory elements. It is highly recommended to review 29 CFR 1910.119(c) through (p) for specific requirements.
Overall, these 14 elements are designed to help facilities identify and control hazards associated with hazardous chemicals, and to ensure the safety of workers and the environment. A brief overview of the 14 elements is provided below:
- Employee Participation: Facilities must establish a system to involve employees in the development and implementation of the PSM program including employee training, participation in process hazard analyses, and development of operating procedures, etc.
- Process Safety Information: Facilities must compile and maintain an extensive suite of information relating to their processes, including safety data sheets, process flow diagrams, piping and instrument diagrams, materials of construction, safety systems, conformance to recognized and generally accepted good engineering practices (REGAGEP), etc.
- Process Hazard Analysis: Facilities must conduct an extensive hazard analysis of their processes to identify potential hazards, evaluate the effectiveness of existing safety measures, assess human factors, etc., and must implement a system to address findings and recommendations.
- Operating Procedures: Facilities must develop and maintain written operating procedures that provide clear instructions for operating each process under various operating scenarios.
- Training: Facilities must ensure that employees involved in operating or maintaining a process are trained in the specific hazards associated with the process and the measures needed to control those hazards.
- Contractors: Facilities must ensure that contractors working on their processes are trained and follow the same safety procedures as their own employees.
- Pre-Startup Safety Review: Facilities must conduct a safety review of any new or modified process and ensure appropriate employee training, etc. prior to start up.
- Mechanical Integrity: Facilities must establish a program to maintain the mechanical integrity of process equipment, including inspections, testing, preventive maintenance, procedures, employee training, etc.
- Hot Work Permit: Facilities must establish a permit system for hot work (e.g., welding, cutting, brazing) to ensure that safety measures are taken to prevent fires and explosions. Note that in practice this element often expands to include references to other OHSA regulations and standard safe work practices (LOTO, Work at Height, Confined Space Entry, etc.).
- Management of Change: Facilities must establish procedures to manage and authorize changes to process chemicals, technology, equipment, and procedures that may affect process safety performance.
- Incident Investigation: Facilities must investigate incidents that result in, or could have reasonably resulted in, a catastrophic release of a hazardous chemical, and establish system to address findings and recommendations.
- Emergency Planning and Response: Facilities must develop and implement an emergency action plan that includes procedures for addressing accidental releases of hazardous chemicals. This plan must meet the requirements of 29 CFR 1910.38 (at a minimum).
- Compliance Audits: Facilities must conduct periodic 3-year compliance audits to evaluate the effectiveness of the PSM program and identify opportunities for improvement, and must establish a system to address findings and recommendations.
- Trade Secrets: This element allows facilities to withhold trade secret information from the PSM program, but does require them to make the information available to employees and contractors who may need it to perform their duties. For example, those job duties may require trade secret information for purposes of Process Hazard Analysis, Operating Procedures, Incident Investigation, Emergency Planning and Response, and Compliance Auditing.
So What Might This Mean for Your Facilities?
So what does this all really mean for you, you might ask? The main takeaway is simple: OSHA's PSM standard provides a robust management system framework for reducing process safety-related risks and ensuring safe workplaces and surrounding communities. If your facility meets or exceeds threshold quantities, your best foot forward is to understand what the PSM standard requires, and what you should do to meet or exceed those requirements. In the blog posts to follow, we'll discuss some best practices and other ideas that will help facilities apply the PSM management system elements effectively to reduce their risk of hazardous chemical releases. In the meantime, here are some suggested steps to follow to help you determine if your facility needs to comply with OSHA's PSM standard:
- Identify and make an inventory, including quantity and type of chemicals stored, used, handled, manufactured, and/or moved at your facility.
- Determine the threshold quantity ((see 29 CFR 1910.119 Appendix A) for any PSM highly hazardous chemicals on your inventory. If your inventory quantity exceeds the associated threshold quantity, then your facility may need to comply with OSHA PSM.
- Identify the processes that involve the storage, use, handling, manufacture, and/or movement of any PSM highly hazardous chemicals on your inventory (see 29 CFR 1910.119(b) for the definition of process). Any identified processes storing, using, handling, manufacturing, and/or moving PSM highly hazardous chemicals at or above their threshold quantity will be subject to and covered by the PSM standard.
- Note that facilities can have more than one covered PSM process/chemical in which case they will need to have multiple PSM programs.
- Review the OSHA PSM requirements (see 29 CFR 1910.119 and note that OSHA’s website includes valuable additional reference materials) to understand the PSM requirements and begin development of your facility’s PSM program. Consult with a qualified EHS professional having OSHA PSM experience if you are unsure whether your facility needs to comply with OSHA PSM or if you need assistance developing and implementing a PSM program.
Read the rest of the series
Read part 2
Read part 3